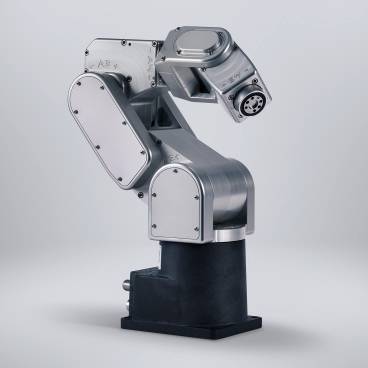
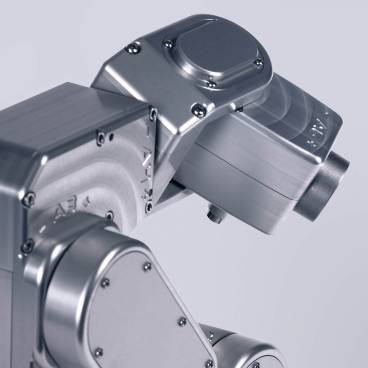
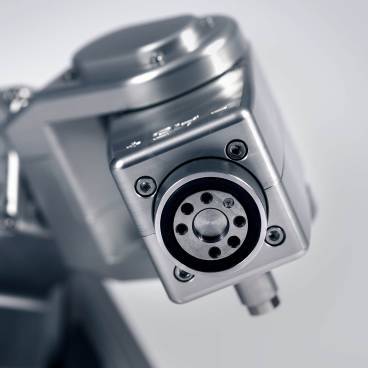
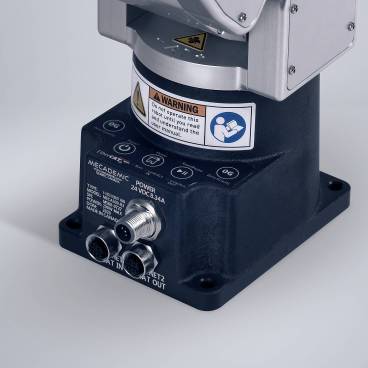
BENEFITS
- Smaller than any industrial robot arm.
- Featuring an embedded controller.
- Unbelievably compact.
- Built with precision-machined aluminum and zero-backlash gearboxes, the Meca500 is the world’s most precise six-axis robot.
- It boasts a repeatability of 5 μm.
- Plug‑and‑work automation component, easy to interface with any computer or PLC.
- Easily operate the robot using any programming language you prefer.
- Easy to mount in any orientation.
- Automatically compensates for gravity, without requiring any software adjustments. This added flexibility enables easy integration in a wide variety of settings.
- Low initial cost – The small industrial robot arm comes with lifetime firmware updates and requires no software licenses.
- No maintenance costs – With 24/7 maintenance-free operation, there is no need for battery or oil replacements.
- Cheaper factory space – Tiny footprint enables a lower space per unit cost.
- Cheaper logistics – Quick and easy integration means reduced installation and training costs.
SPECIFICATIONS
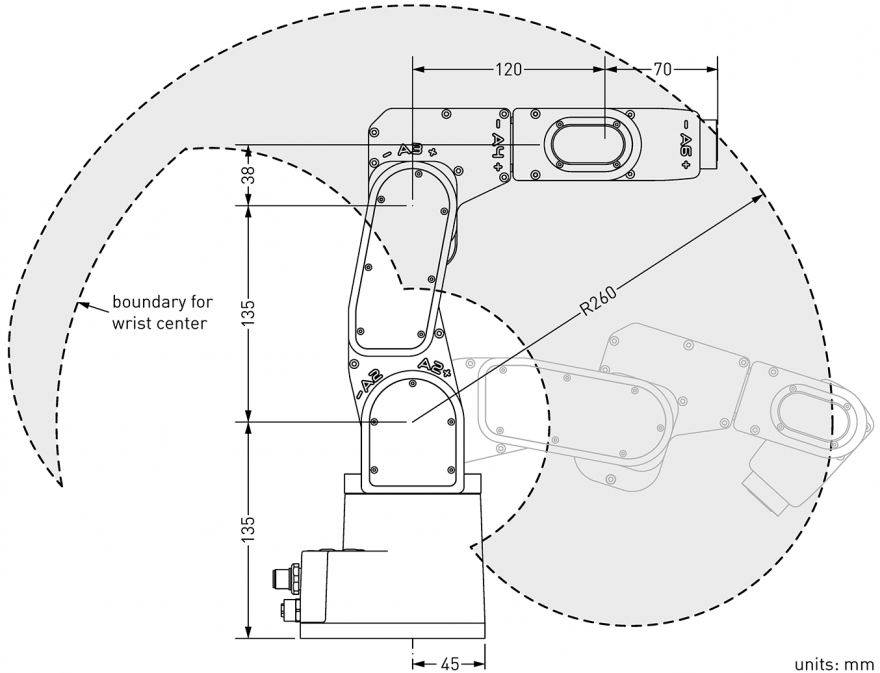
- When fully extended, the length of the small industrial robot arm is about 330 mm.
- Reach: 330 mm
- Payload: 0.5 kg rated (max. 1 kg)
- Weight: 4.6 kg
- Mounting: any orientation
CONTROLLER
- The Meca500’s controller is embedded in its palm-sized base. There is no bulky controller cabinet, no teach pendant, and no messy cables. With its tiny footprint, the Meca500 is ideal for small, confined spaces.
PRECISION
- Our precision robot arm is equipped with the market’s highest quality zero-backlash speed reducers and high-resolution encoders. Its structural components are precision machined, precision assembled, and inspected at Mecademic. The robot features unmatched repeatability.
- Repeatability: 0.005 mm
OPERATION
- Simply connect the robot to any computer or PLC via the Ethernet cable provided, and use a programming language of your choice (Java, C#, Python, etc.). The robot can also be controlled by most PLCs using either Ladder or Structured Text.
- Users may communicate with the robot via EtherCAT, ensuring guaranteed response times. Alternatively, users may send Mecademic’s proprietary commands to the robot arm (as parsed strings) over TCP/IP. The commands are typical robot instructions such as MoveLin(x,y,z,α,β,γ). Similarly, the robot’s controller sends back strings with various types of feedback.
- The robot’s controller features an intuitive web interface for operation. It can be accessed via any web browser.
- Communication protocols: PROFINET (see certificate), Ethernet/IP (see certificate), EtherCAT, TCP/IP
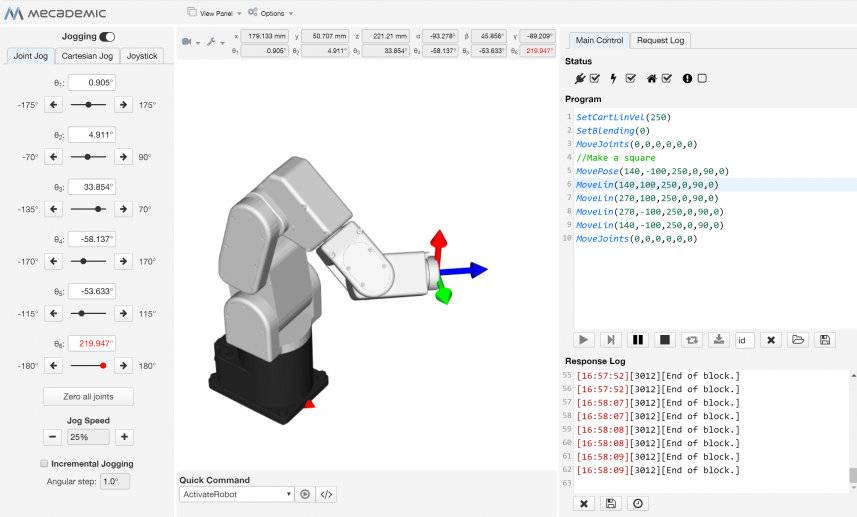
POWER SUPPLY AND SAFETY
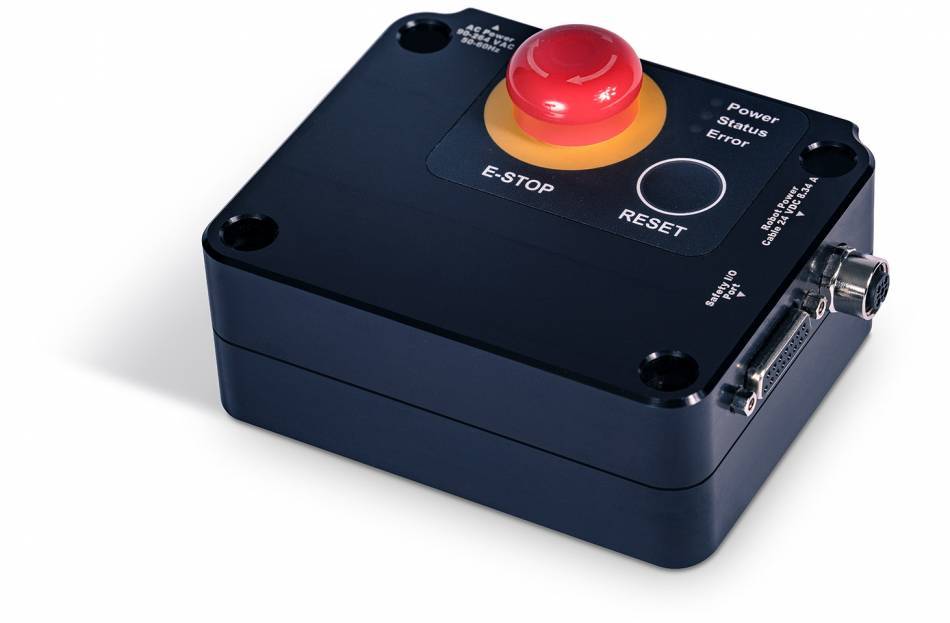
- The Meca500 comes with an external 24V power supply that has an embedded safety module with an E-Stop and safety I/O interface. The power supply can be connected to any standard electrical outlet.
- Supply voltage: 90-264VAC, 50-60 Hz, single phase
- Safety module: Cat. 3 / PL d